Systèmes de gestion de batterie sans fil?: des solutions pour écosystèmes intelligents qui améliorent les performances, allongent la durée de vie et optimisent le coût des batteries.
Par Stephan Prüfling, chef de produit en charge des systèmes de gestion de batterie (BMS), AVL?; et Norbert Bieler, directeur du développement, Mobilité électrique (E-Mobility, Analog Devices, Inc).
Introduction
L’électrification des berlines et des véhicules utilitaires entre actuellement dans une nouvelle phase de pénétration du marché. Alors que la démonstration de faisabilité de la technologie fait place à la production en série de véhicules haut de gamme, l’accès à de nouvelles technologies permet de proposer des véhicules optimisés à un coût nettement plus abordable.
Néanmoins, la plupart des véhicules électriques de génération actuelle sont encore considérés comme trop onéreux et moins attrayants que leurs homologues équipés d’un moteur classique à combustion interne. Face à ce constat, la baisse des coûts et l’amélioration des performances constituent deux critères déterminants pour durabiliser la croissance du marché. Ainsi, alors que la réduction des dimensions, du poids et du coût influence de façon significative la compétitivité des systèmes de batteries tout au long du cycle de vie des véhicules, l’extension de l’autonomie aura une influence notable sur leur compétitivité et leur attractivité commerciale. Sans oublier qu’à l’heure où un nombre croissant de véhicules électriques arrivent en fin de vie, les constructeurs vont entrer en concurrence à propos de la valeur qu’ils parviennent à donner aux batteries de seconde vie extraites des VE mis au rebut.
Dans ce contexte, les informations relatives aux innovations apportées aux batteries portent essentiellement sur les nouveaux concepts de conditionnement des batteries, ainsi que sur les nouveaux matériaux susceptibles à terme de stocker davantage d’énergie que le lithium. Un autre organe a tendance à échapper au radar, alors qu’il doit suivre et accompagner ces innovations?: le système de gestion de la batterie (BMS), dont le rôle consiste à surveiller l’état de charge (SoC — State of Charge) et l’état de santé (SoH — State of Health) des batteries.
À ce titre, le nouveau système de gestion de batterie BMS sans fil (wBMS — wireless BMS) mis au point par Analog Devices et utilisé pour la première fois par General Motors dans sa plateforme de batterie modulaire Ultium est à présent produit en série. Avec la technologie wBMS, les constructeurs automobiles disposent d’un nouvel atout compétitif d’un bout à l’autre du cycle de vie des batteries, de l’assemblage initial des modules jusqu’à l’utilisation à bord d’un véhicule électrique en passant par la mise au rebut, voire à l’exploitation en seconde vie.
Batteries câblées?: une approche coûteuse, lourde et complexe
La technologie wBMS est née de l’analyse des inconvénients du câblage utilisé pour connecter les blocs-batterie conventionnels qui équipent actuellement les VE. Cette analyse s’est appuyée sur l’expertise acquise par ADI, fournisseur des circuits intégrés de gestion de batterie (BMS) les plus précis du marché pour le secteur des communications sans fil. ADI a par ailleurs développé la plus robuste des technologies de réseau maillé pour environnements industriels.
Dans un bloc-batterie pour VE classique, chaque élément est mesuré par un circuit intégré de gestion de batterie. Les données collectées sont transmises à l’unité de commande électronique (ECU — Electronic Control Unit) du pack via une liaison filaire. Cette solution de communications interne témoigne de la complexité de l’architecture des blocs-batterie de grandes dimensions?: un bloc-batterie se compose généralement de nombreux modules contenant chacun plusieurs éléments. En raison des variations de production naturelles, chaque élément présente des caractéristiques particulières qui varient dans une plage de tolérance spécifiée. Pour optimiser la capacité, la longévité et les performances de la batterie, les principaux paramètres opérationnels?— tension, courant de charge/décharge, et température?— doivent être surveillés et enregistrés séparément pour chaque module.
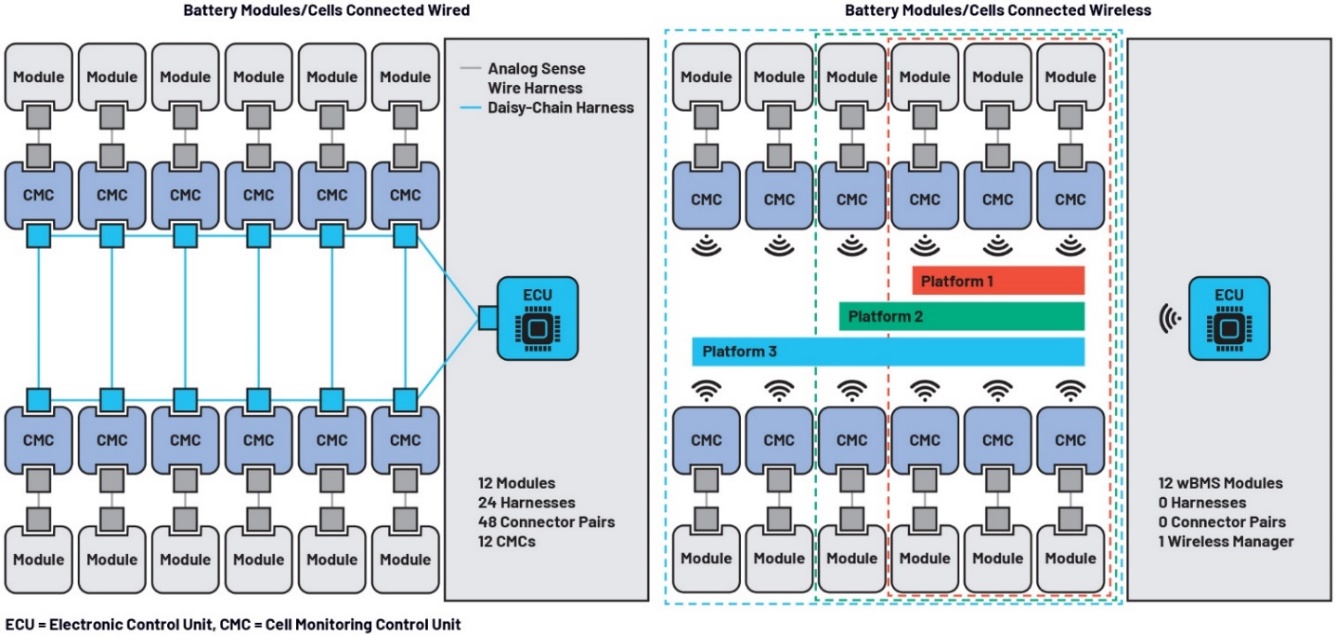
C’est pour cette raison que la batterie d’un VE doit disposer d’un moyen de transférer les données entre les différents modules ou éléments (mesure de la tension et de la température) et le processeur de l’ECU (Figure?1). De manière générale, ces connexions réalisées au moyen de câbles présentent l’avantage d’être utilisées couramment et, par conséquent, maîtrisées par les concepteurs.
Inconvénients des systèmes câblés
Les inconvénients liés aux connexions filaires ne manquent toutefois pas?: un faisceau de câbles en cuivre augmente le poids de l’ensemble et occupe un espace qui, s’il était rempli par un élément de batterie, délivrerait un supplément d’énergie. De plus, le câblage doit être fixé à la structure du boîtier de la batterie, tandis que les connecteurs sont potentiellement sujets à des défaillances mécaniques, sous l’effet notamment des vibrations et des chocs.
En d’autres termes, l’utilisation de fils complique la tâche des développeurs, et augmente le coût de fabrication et le poids tout en réduisant la fiabilité mécanique et l’espace utile, avec pour conséquence une réduction du rayon d’action du véhicule. En supprimant les faisceaux de câbles, les constructeurs automobiles bénéficient d’une flexibilité accrue pour répondre aux exigences de conception et de format de leur bloc-batterie.
La complexité des faisceaux de câblage des batteries contribue par ailleurs à augmenter le coût et la difficulté d’assemblage des packs de batteries?: les blocs câblés doivent en effet être assemblés et les connexions branchées manuellement, un processus aussi onéreux que dangereux, dans la mesure où les modules de batterie forte tension des VE sont fournies chargées. Pour maintenir la sûreté du processus d’assemblage et protéger les opérateurs présents sur la chaîne de fabrication, il importe d’appliquer des protocoles de sécurité rigoureux.
On le voit, les OEM ont de bonnes raisons d’adopter une technologie sans fil robuste dans leurs les nouvelles plateformes de systèmes de batteries pour véhicules électriques.
wBMS?: une nouvelle approche connectée
La technologie wBMS est une solution de gestion de batterie sans fil complète que les constructeurs automobiles peuvent intégrer aisément dans leurs packs de batteries. Un système wBMS se compose d’un circuit de surveillance sans fil des éléments de batterie (wCMC) associé à chaque module de batterie et d’une unité de gestion sans fil qui pilote le réseau de communications et relie plusieurs modules de batterie sans fil à l’unité de commande électronique (ECU). Outre la section « wireless », chaque unité wCMC intègre un système BMS qui mesure divers paramètres avec une très grande précision pour que l’unité de traitement des applications puisse analyser l’état de charge et l’état de santé (SoC/SoH) des batteries.
Si la technologie wBMS tire pleinement parti de l’élimination du problème que représentent la conception et l’assemblage des faisceaux de câbles, il est possible de générer davantage de valeur encore à d’autres phases du cycle de vie des batteries?:
• assemblage de la batterie — les seules connexions dont a besoin un module de batterie sont les bornes d’alimentation, lesquelles peuvent facilement être traitées selon un processus hautement automatisé. L’élimination des tâches manuelles d’assemblage et de tests évite en outre les risques liés à la sécurité des opérateurs présents sur les chaînes de montage (figure?2). De plus, les modules peuvent également être testés et appariés avant leur installation à l’intérieur de la batterie?;
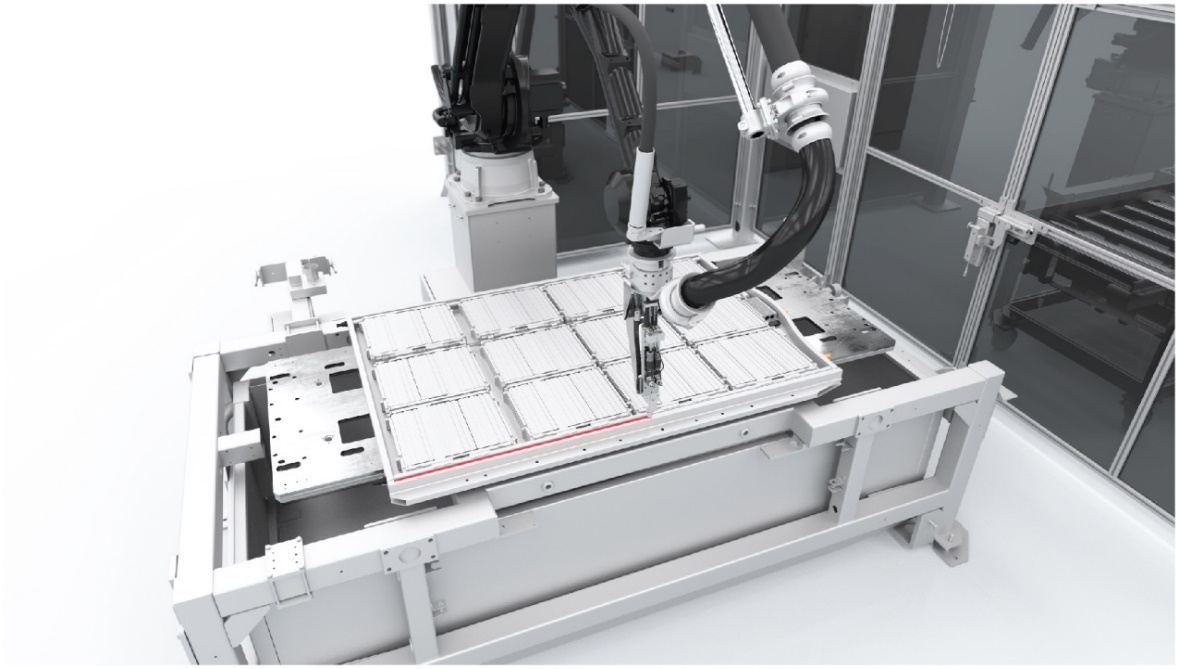
• entretien — grâce au mode sans fil sécurisé, l’état du pack de batteries peut être analysé sans difficulté dans un garage agréé à l’aide d’un équipement de diagnostic, sans intervenir au niveau du pack. En cas de dysfonctionnement, le module défaillant sera facilement déposé et remplacé. Enfin, la configuration «?sans fil?» simplifie l’installation de nouveaux modules dans le système de batterie?;
• seconde vie — l’évolution du parc de véhicules électriques va de pair avec l’émergence d’un marché pour les batteries de seconde vie qui sont extraites des automobiles mises au rebut en vue de leur réutilisation dans des applications telles que les systèmes de stockage d’énergie renouvelable ou des outils électriques. Cette approche représente une nouvelle source de valeur pour les fabricants de VE auxquels il incombe de recycler ou d’éliminer les batteries des VE mis au rebut, dans la mesure où la technologie sans fil wBMS simplifie l’intégration des modules dans les applications de seconde vie?;
• mise au rebut — les métaux recyclables et les matériaux potentiellement nocifs que l’on trouve à l’intérieur des blocs-batterie imposent des mesures d’élimination approuvées et règlementées. Par rapport aux batteries câblées, les connexions simplifiées et l’absence de faisceaux de câbles simplifient et accélèrent l’élimination des modules de batterie.
• gestion des données — la technologie wBMS facilite la lecture des données critiques à partir de chaque module intelligent?: en d’autres termes, l’état des batteries peut être déterminé de façon individuelle. Ces données fournissent, par exemple, des indications relatives à l’état de charge (SoC) ou de santé (SoH) d’un module. Associées aux données créées lors de la fabrication initiale du module, ces informations favorisent une utilisation optimale dans le cadre d’une deuxième vie, ainsi que la fourniture d’un ensemble détaillé de spécifications pour chaque module vendu. La disponibilité immédiate de ces données accroît sensiblement la valeur de revente des modules.
Systèmes wBMS?: des solutions complètes signées ADI
Le protocole de connectivité sans fil mis en œuvre par ADI dans son système wBMS répond aux exigences de l’industrie automobile sur le triple plan de la fiabilité, de la sûreté et de la sécurité, toutes conditions d’exploitation confondues, grâce à la technologie de synchronisation temporelle déployée à l’échelle du réseau. L’utilisation du wBMS dans les véhicules électriques de série commercialisés par General Motors démontre la fiabilité de ce système sans fil dans les environnements les plus exigeants?: une batterie pourvue d’un wBMS a parcouru des centaines de milliers de kilomètres à bord d’une centaine de véhicules d’essai, sur route et hors route, dans les conditions les plus difficiles et des environnements aussi variés que le désert ou les terres gelées du Grand Nord.
Avec son système de gestion de batterie sans fil, ADI participe également aux programmes des constructeurs automobiles conformément à la norme de sécurité fonctionnelle des véhicules routiers ISO?26262. La technologie radio et le protocole de connectivité ont été développés de telle sorte que le système puisse résister aux environnements bruyants et autoriser des communications sécurisées entre les unités de surveillance et le circuit de gestion grâce à une technologie de chiffrement sophistiquée. Les mesures de sécurité évitent le piratage des données échangées sur le réseau sans fil par un utilisateur malintentionné, un cybercriminel ou un hacker. En outre, les données transmises sont reçues sans modification de leur contenu, et le destinataire légitime connait avec précision la source du message.
Gérer la valeur de la batterie tout au long de son cycle de vie
Pendant toute la durée de vie du bloc-batterie — c’est-à-dire de l’assemblage initial à la seconde vie en passant par la mise au rebut, la fonction de gestion sans fil intégrée permet au constructeur du véhicule et à son propriétaire de suivre facilement l’état de la batterie, d’en maintenir les performances et la sécurité, ainsi que d’en maximiser la valeur. L’ensemble du système, y compris les interactions entre le calculateur et les unités de surveillance des éléments incorporeés aux modules de batterie, est piloté par la technologie ADI, les paramètres de configuration étant définis par le constructeur.
La technologie wBMS bénéficie par ailleurs de la technologie BLIS (Battery Lifecycle Insight Service) d’ADI qui fournit un logiciel de traitement de données en périphérie de réseau (edge) et sur le cloud pour optimiser la traçabilité, l’optimisation de la production, la surveillance du stockage et du transit des données, la détection précoce des défaillances et l’extension de la durée de vie. L’utilisation conjointe des technologies wBMS et BLIS permet aux constructeurs automobiles de rentabiliser les investissements consacrés au développement et à la production de packs de batteries, d’améliorer la rentabilité économique de leur stratégie en matière des véhicules électriques, et de contribuer à accélérer la transition du marché vers une mobilité personnelle bas carbone et durable.
La clé de la conception et de la mise en œuvre de solutions de batteries dotées d’un système wBMS réside dans la compréhension du système, ainsi que dans l’utilisation de méthodes et d’outils en appui de la conception et des technologies, comme nous l’avons vu précédemment. Leader dans le développement, la simulation et les tests dans le secteur automobile, AVL propose une gamme complète d’outils de simulation et de test, ainsi que des moyens techniques et une riche expérience pour mener ces innovations à bien en collaboration avec ses clients et les lancer sur le marché en les préparant à la production en série. AVL travaille actuellement sur des solutions destinées à l’écosystème des batteries en développant des méthodologies d’analyse de données, des fonctionnalités prédictives développées en environnement virtuel, et des données relatives aux véhicules et aux batteries afin de prolonger la durée de vie et les performances des batteries.
En collaboration avec Analog Devices, AVL met tout en œuvre pour fournir à ses clients du monde entier des solutions de gestion de batterie plus intelligentes qui réunissent les atouts des deux sociétés.
À propos des auteurs
Stephan Prüfling, M.Sc., a étudié l’ingénierie industrielle et le génie électrique en se concentrant sur la mobilité électrique (e-mobility) et les réseaux d’énergie. Il a rejoint AVL en 2016 et occupe le poste de Chef de produit pour les solutions de transmission électrique (e-drive) telles que les moteurs électriques et les composants d’électronique de puissance. Actuellement, il se concentre essentiellement sur la gestion des produits utilisés dans les solutions de gestion des batteries, ainsi que sur les projets d’innovation dans ce domaine.
Ingénieur électricien spécialisé en microélectronique, Norbert Bieler possède 25 ans d’expérience en gestion automobile acquise chez Siemens VDO, Continental Automotive et Analog Devices. Son expertise porte sur les systèmes, les architectures et les fonctions des véhicules, ainsi que sur l’électronique de l’habitacle, le châssis et la transmission. Ces 15 dernières années, Norbert Bieler s’est concentré sur l’hybridation et l’électrification de l’ensemble du groupe motopropulseur. Il dirige le développement commercial et la stratégie, ainsi que les projets de mobilité électrique qui définissent les nouvelles technologies et innovations des constructeurs automobiles, des sous-traitants de rang?1 et des réseaux de partenaires stratégiques.
Source : com-trail.fr